Upangaji wa Baadaye Unaponunua Vifaa vya Ufungaji
Kununua vifaa vya upakiaji kwa mradi mpya kunaweza kuchukua muda, gharama kubwa, na hata kutatanisha ikiwa mchakato huo ni mpya kwa mnunuzi. Kuna chaguo nyingi tofauti hata ndani ya kitengo cha mashine moja, na ukosefu wa uzoefu na ujuzi unaweza kufanya iwe vigumu kuchagua vifaa bora kwa kazi. Kwa bahati mbaya, kwa wengi ambao ni wapya katika upakiaji wa bidhaa, iwe pombe iliyoyeyushwa, maji ya chupa, shampoo, au bidhaa nyingine yoyote, maneno kama vile kanuni za kufurika, vifunga vifungashio, na vifungaji vya induction huenda visiwe na maana sana. Watengenezaji wa mashine za ufungaji wanaweza kusaidia vifurushi vipya na kazi hii, lakini uchanganuzi wa mahitaji ya ufungaji haupaswi kuacha katika kuchagua aina sahihi ya mashine.
Ununuzi wa awali wa mashine za ufungaji unapaswa kufanywa kila wakati kwa kuzingatia siku zijazo ili kuokoa pesa na wakati wa mfungaji. Wafungaji wengi wa vifurushi wanafahamu mahitaji ambayo lazima yatimizwe mara tu uzalishaji unapoanza. Walakini, kujenga laini ya ufungaji ambayo inakidhi mahitaji hayo tu kawaida ni kosa kubwa. Lengo kuu la takriban kila kifurushi ni kukua au kupanua, kuongeza nafasi ya rafu au kupanua maeneo ya usambazaji. Kwa kutarajia ukuaji wa siku zijazo, vifaa vya ufungaji vinaweza kujengwa ili kuwezesha ukuaji huo na kuzuia hali ya kuwa na mashine zisizo na maana mwaka mmoja au miwili chini ya barabara. Kama ilivyoelezwa hapo juu, gharama za vifaa zinaweza kuwa gharama kubwa, haswa kwa mifumo ya kiotomatiki, kwa hivyo vifurushi vipya vinahitaji kusawazisha hitaji lao la mtiririko wa pesa wa sasa na hamu yao ya kununua vifaa na maisha marefu yanayotarajiwa.
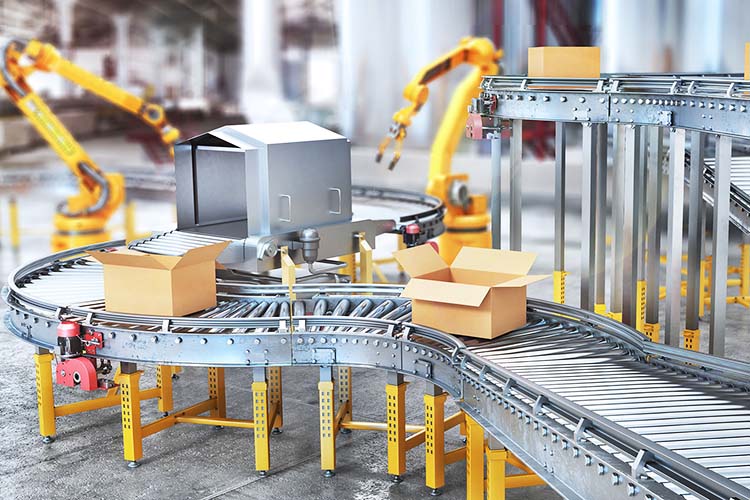
Mambo ya kuzingatia unaponunua mitambo ya vifungashio na kupanga kwa ajili ya siku zijazo
- Bidhaa tofauti na ufungaji - Ni salama kusema kwamba karibu mashine zote za upakiaji zimebinafsishwa kwa mradi uliopo. Saizi na maumbo tofauti ya kontena, aina tofauti za kofia, mnato wa bidhaa, na mambo mengine yote yanaweza kuathiri jinsi laini ya upakiaji inavyoundwa. Kumbuka kwamba ikiwa unapanga kuzindua bidhaa tofauti au hata kifurushi tofauti cha bidhaa sawa, mashine zilizopo za upakiaji lazima ziweze kushughulikia nyongeza hizi, au laini mpya kabisa itahitajika. Kwa mfano, ikiwa kifurushi kinaanza na chupa ndogo za wakia moja au mbili lakini anataka kuongeza chupa kubwa zaidi katika siku zijazo, wanapaswa kuwa waangalifu ili kuhakikisha kuwa mfumo wa kupitisha umeme unaotumiwa unaweza kurekebishwa ili kushughulikia vyombo vikubwa zaidi. Vile vile ni kweli kwa mashine tofauti za ufungaji, kama vile mashine za kujaza au vifaa vya kuweka alama zilizotajwa hapo juu.
- Kasi – Bila shaka, jinsi mashine inavyofanya kazi kwa kasi, ndivyo mahitaji ya uzalishaji yanavyoweza kutimizwa yanavyoongezeka. Hitilafu moja ni kununua vifaa vya ufungaji vinavyokidhi mahitaji ya sasa. Kwa mfano, mashine ya kujaza inaweza kuwa na uwezo wa kujaza chupa hamsini kwa dakika na vichwa kumi vya kujaza, ambayo inakidhi mahitaji ya sasa ya bidhaa. Hata hivyo, kwa kuongeza tu bandari kwenye makopo na baa za kujaza, vichwa vya ziada vya kujaza vinaweza kuongezwa katika siku zijazo ili kukidhi mahitaji ya juu. Katika hali nyingine, kampuni inaweza kununua kichujio cha nusu otomatiki ili kukidhi mahitaji ya ujazo wa chini hadi wa kati. Kichungi kama hicho kinaweza kujengwa kwa sura sawa na kichungi cha kiotomatiki, na vifaa vinaweza kushughulikia viwango vya juu katika siku zijazo ikiwa inataka.
- Nafasi - Mahali halisi ya mwili ya mashine ya ufungaji inapaswa kuzingatiwa kila wakati. Kampuni zinazoanza uzalishaji na mashine za kujaza na kuweka alama huenda zisihitaji sakafu kubwa ya uzalishaji. Kwa kweli, mashine za ufungaji zinaweza kujengwa kufanya kazi kwenye meza ya meza au mfumo wa fremu moja. Hata hivyo, ikiwa kampuni inaendesha michakato yake sehemu moja kwa wakati, kumbuka kwamba vifaa vya ziada vitahitaji nafasi ya ziada. Vile vile, kampuni zilizo na mifumo otomatiki kikamilifu zinaweza kutaka kuongeza vifaa vya usaidizi kama vile rekodi, vifungaji vya induction, mikanda ya shingo au vifaa vingine. Vifaa vingi vya kiotomatiki vinaweza kuzungushwa kwenye mfumo uliopo wa conveyor na vinaweza kuunganishwa kwa urahisi kwenye mfumo uliopo ikiwa nafasi inapatikana. Conveyors inaweza kuunganishwa ili kuongeza nafasi ya mstari.
Kujipa uhuru katika suala la kasi, upeo na nafasi huruhusu mifumo ya upakiaji kupanua maisha yao wenyewe na kuokoa wafungaji wakati na pesa zinazohitajika kununua vifaa vipya kwa sababu ya ukosefu wa uchanganuzi. Msisimko wa kuanzisha mradi au biashara mpya itafifia haraka ikiwa gharama zisizo za lazima za vifaa vya ufungaji zinarejeshwa mwaka baada ya mwaka.